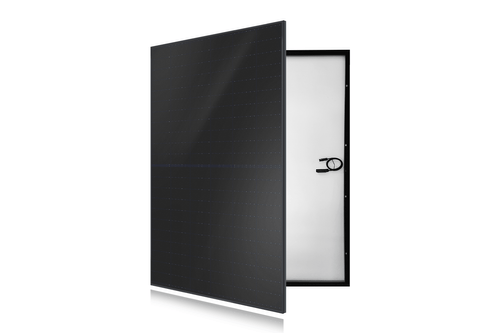
IBC Black Solar Panels Mono-Facial 60 Solar Cells 375W-385W Solar Modules
Power: 375W 380W 385W
Dimension (L × W × T): 1720 × 1039 × 35mm
Packing: 30pcs/pallet, 780pcs/40"HQ
1. All new battery technology, all black appearance design, suitable for specific installation scenarios.
2. No grid line design on the front side, effectively increasing the light receiving area and improving power output.
3. Advanced cell technology has a high conversion efficiency, effectively increasing the module power output.
4. The grid lines of the cells are on the back side, reducing the circuit distance and lowering the series resistance.
1.The most distinctive feature of the IBC solar cell is that both the PN junction and the metal contact are on the back side of the solar cell. The front surface completely avoids the shading of the metal grid wire electrodes and, in combination with the light trapping structure consisting of a pyramidal suede structure and a reflection-reducing layer on the front surface, is able to maximise the use of incident light, reduce optical losses and have a higher short-circuit current. At the same time, an optimised metal grid electrode is used on the back to reduce the series resistance. A SiNx/SiOx double layer film is usually used on the front surface, which not only has a reflection reduction effect, but also has a good passivation effect on the suede silicon surface. At present, IBC cells are the most complex process and the most difficult structure design among commercial crystalline silicon cells. HBC technology using a combination of IBC and HJT technology allows for further improvements in cell efficiency, having already obtained a world record efficiency of 26.6% in 2017.
2. The process of IBC cells is much more complex than that of conventional solar cells, and the key issue in the IBC cell process is how to prepare the P and N zones on the backside of the cell in a forked-finger arrangement, and to form metallisation contacts and grid lines on top of them respectively. For diffusion, furnace tube diffusion is by far the most widely used method. While diffusion in normal solar cells only requires the formation of N-type diffusion zones on a P-type substrate, IBC cells have both phosphorus diffusion to form the back-side N zone (BSF) and boron diffusion to form the PN junction, i.e. P-type doping on an N-type substrate.
3. Electrically, the performance of IBC cells is more affected by the front surface than conventional cells, as most of the photogenerated carriers are generated at the incident surface and these need to flow from the front surface to the back of the cell up to the contact electrode, therefore, better surface passivation is required to reduce carrier compounding. To reduce carrier complexation, the cell surface needs to be passivated. Surface passivation reduces the density of surface states and is usually available as a chemical or field passivation. One of the more popular applications of chemical passivation is hydrogen passivation, such as H-bonding in SiNx films, which enters the silicon under the action of heat to neutralise the hanging bonds on the surface and passivate the defects. Field passivation uses the shielding effect of a fixed positive or negative charge in the film on the minority carriers, such as a positively charged SiNx film, which attracts negatively charged electrons to the interface. In N-type silicon, the minority carriers are holes and the positive charge in the film has a repulsive effect on the holes, thus preventing them from reaching the surface and being compounded. Therefore, positively charged films such as SiNx are more suitable for passivation of the N-type silicon front surface of IBC cells. For the back surface of the cell, where there is both P and N diffusion, the ideal passivation film is one that passivates both the P and N diffusion interfaces, and silica is a better choice. If there is a large proportion of Emitter/P+Si on the backside, a negatively charged film such as AlOx is also a good choice.
4. One of the core technologies of IBC cells is the design of their backside electrodes, as it not only affects the cell performance, but also directly determines the process of making the IBC module. Depending on the electrode design, IBC cells comprise three main types. IBC cells without a main grid. This is characterised by the fact that only thin grid lines are printed on the back side, eliminating the need for printed insulating adhesive and main grid. However, this type of IBC cell requires special equipment to support the fabrication of the module and has high precision requirements, resulting in higher costs on the module side. Four main grid IBC cells. It is characterised by the fact that modules can be made using conventional welding methods with low accuracy requirements, no specialised equipment is required and it is highly applicable. However, the cell preparation process requires the printing of insulating adhesive and the main grid, making the cell process relatively complex. Spot-connected IBC cells. It is characterised by the fact that no insulating glue needs to be printed and the main grids are printed in a single pass, making the cell process simple; the cells are interconnected using metal foil during the fabrication of the module and the accuracy requirements are lower than for the non-grid type.
5. Below are the specifications for our IBC 375W~385W components, which can be downloaded at any time by clicking on the links.
Click the icon below to get a quote